The Role of Rider Castings in Steel Mills
Rider castings are found in several critical areas of the steel production process. Their main functions include:
Supporting and Guiding Equipment: Rider castings often act as support structures in rolling mills or similar equipment, guiding and stabilizing heavy steel products as they move through various stages of production. This is especially important in rolling mills, where hot steel billets or slabs are shaped by rollers and moved through high-temperature zones. By maintaining alignment and offering steady support, rider castings help to ensure that equipment operates smoothly and without interruption, preventing misalignments that could lead to defects in the steel or cause damage to machinery.
Load-Bearing Capacity: Many rider castings are designed to bear significant loads. Whether used in overhead cranes, transfer carts, or conveyors, these castings are built to handle the immense weight of raw materials and finished steel products. The strength of the casting material is crucial for providing the necessary load-bearing support during heavy-duty operations, preventing cracks, deformation, or failure.
Thermal and Abrasion Resistance: Steel mills operate at extreme temperatures, often exceeding 1,000°C (1,832°F). Rider castings need to withstand thermal shock and continual exposure to high heat without losing their structural integrity. Furthermore, these castings are subject to abrasive wear from direct contact with steel and other hard materials, requiring high wear resistance. Special high-alloy materials and heat-resistant coatings are often used in rider castings to prolong their service life and maintain their performance even in the harshest conditions. This resistance to heat and wear is vital for reducing maintenance costs and minimizing equipment downtime.
Minimizing Vibration and Stress: In steel mills, machinery is constantly in motion, with heavy equipment subject to significant vibrations and mechanical stresses. Rider castings help to dampen vibrations and distribute these stresses more evenly across the structure, preventing damage to both the steel products and the machinery. This is particularly important in rolling mills, where the pressure exerted on the steel during shaping can cause mechanical shocks. By stabilizing the moving parts, rider castings help to reduce the likelihood of structural failure or misalignment caused by excessive stress or vibration.
Thank you for considering us for your next alloy purchase.
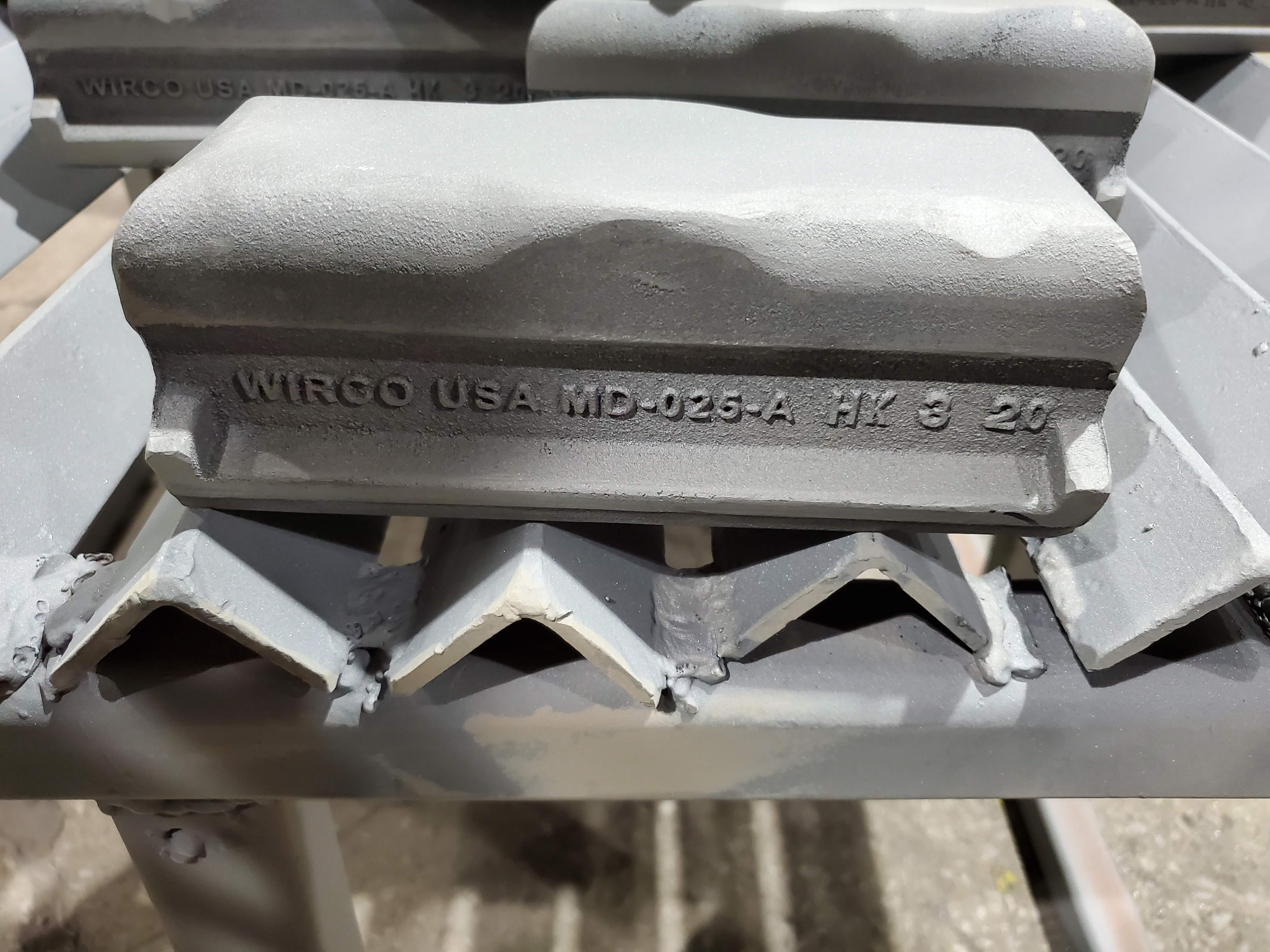
We thank you for your business and hope you consider Wirco for your next alloy purchase.